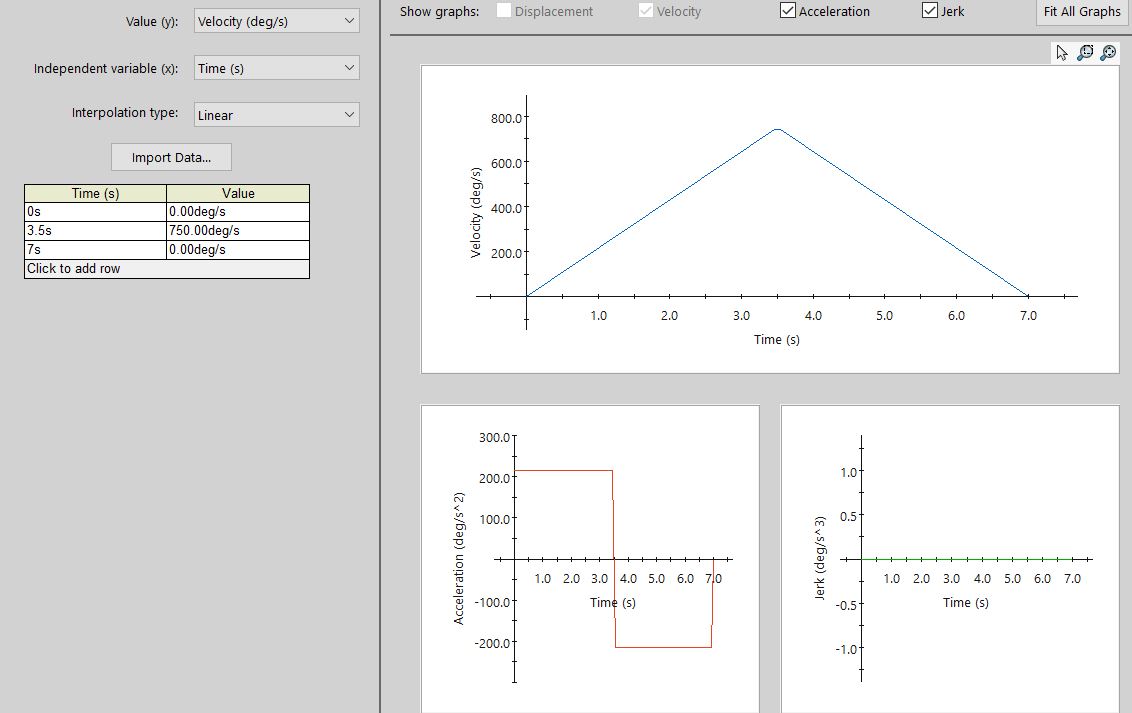
Design & Simulation:
-
Created an initial cart concept individually in SOLIDWORKS, using Motion Analysis to simulate performance.
-
The prototype featured a sled design pulled via a Rack and Pinion system, achieving a 10-ft run in 7 seconds at a peak velocity of 800°/sec.
-
Early design iterations lacked rubber padding, which could have improved stability and speed by increasing surface friction.
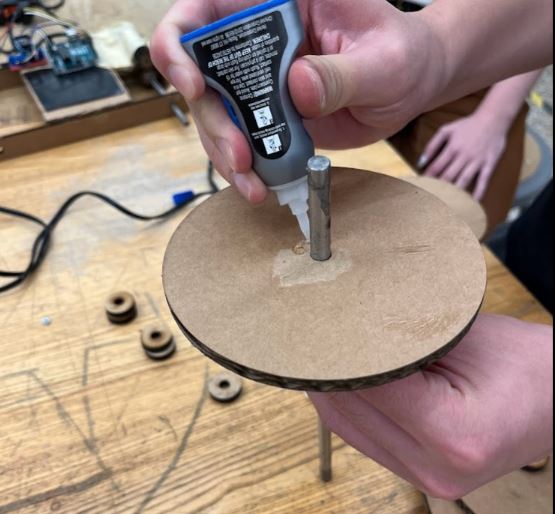
Fabrication:
-
Constructed using cardboard and plywood from EPIC stock; critical components (wheels, gears, spacers) were laser cut.
-
Hot glue was used for cardboard connections, and super glue for wooden spacers and friction pad attachment.
-
The motor system (including DC motor, H-Bridge, and Arduino) was secured with painter’s tape.
-
The drivetrain featured axles and a gear system, a pivot from the original plan to use a 3D-printed spool that wasn’t completed in time.
One major design change was that we were initialy going to 3D print a spool and use that to pull the cart. However, since the print was not done by Monday, we instead had to change to using gears to power the cart like a car rather than pulling it.
Testing & Performance:
-
Final prototype transported the foot-long aluminum bar across 10 feet in 5.5 seconds, outperforming all other teams.
-
Demonstrated system stability and consistent performance under load, with the rubber pad significantly improving grip.